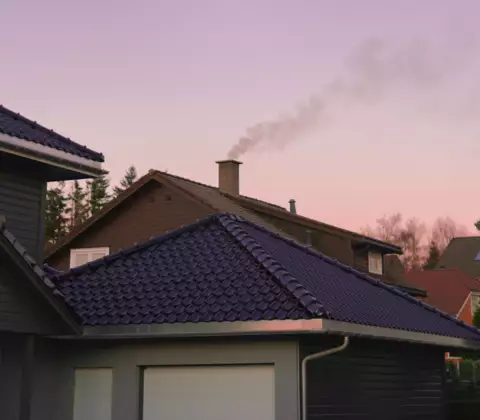
Net and gross calorific value
Differences and advantages
A high level of energy efficiency is particularly important nowadays. More and more homeowners are relying on the installation of modern heating systems, not only for environmental protection but because heating costs can often be reduced significantly by taking appropriate measures. The investments therefore pay for themselves after a more or less short period of time.
Especially when retrofitting older heating systems in old buildings, switching to condensing technology can bring great benefits, and the existing heating system can continue to be used to a large extent. But what is the difference between net calorific value (NCV) and gross calorific value (GCV)?
What is the difference between net calorific value and gross calorific value?
If you as a home owner or builder research the possibilities of installing or upgrading modern heating systems, you inevitably come across the terms net calorific value (NCV) and gross calorific value (GCV), often without more detailed explanations of what they mean.
Even in some personal consultations, the contractors sometimes assume that customers are already familiar with the subject. At WOLF you can rely on receiving excellent advice.
Regardless of whether it’s oil heating, gas heating, heat pumps or solar thermal: If you have specific questions or requests, the WOLF hotline will be happy to help you.
While the NCV only reflects the energy content of a fuel, the GCV indicates how much thermal energy can be obtained in total by the heating system. Condensing technology uses the energy of the combustion gases to generate additional heat.
The higher the NCV and GCV, the better for energy efficiency. Conventional heating technology, on the other hand, allows the exhaust gases to escape into the atmosphere without using their thermal energy.
How does condensing technology work?
Net calorific value
In a conventional boiler, only the net calorific value of the respective fuel is used, regardless of the source material. This applies to both old constant temperature systems and low temperature boilers.
Heating industry professionals speak of dry combustion because condensation of water vapour contained in the exhaust gases is prevented. Relatively high temperatures are required for this, which is why the exhaust gas temperature is significantly higher with pure net calorific value systems.
In the case of condensing technology, in addition to the net calorific value, the energy that is released when the exhaust gases are cooled is also used. We know this from other systems such as the refrigerator or the cooling system in a car: heat exchangers extract heat from the coolant and thus lower the temperature.
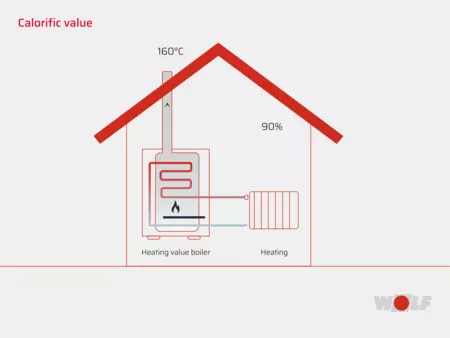
Gross calorific value
A similar effect is used in condensing boilers. When water vapor transitions from the gaseous to the liquid state, heat is released. If this is condensed in the heating system, the waste heat can be used efficiently. This additional heat in turn enters the heating circuit.
The energy lost as unused heat is released into the environment via the flue stack are thus greatly reduced. One hundred percent avoidance of flue gas losses is not possible in practice, even with condensing technology, as there will always be a certain amount of loss via pipelines and secondary cooling effects.
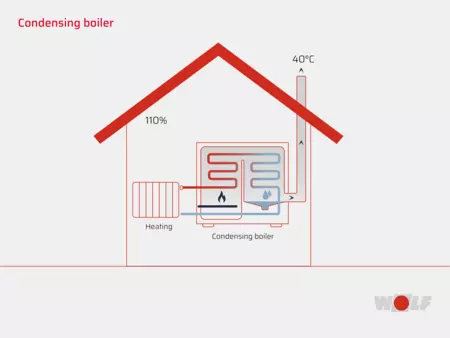
Use of condensation in condensing boiler technology
Boilers with condensing technology take advantage of the principle of condensation heat since when gas, oil or wood is burned, there is always a certain amount of water vapour in the flue gases. Depending on the fuel, the dew point at which the exhaust gases liquefy again differs, and therefore so does the heat that can be extracted.
The value for natural gas is around 57 °C, while for heating oil it is around 10 °C lower. This means that the waste heat from natural gas can be used more quickly because the cooling of the exhaust gases to 57 °C is faster than to 47 °C. In this respect, the fuel also determines how much energy the heating system can deliver.
You can assess this based on the energy parameters of the fuels. The more standardised a fuel, the more precisely the energy parameters can be determined. In some cases, the values for wood fluctuate extremely because factors such as density and moisture vary greatly depending on the type of wood.
In the case of fuels such as heating oil or natural gas, the differences are easier to quantify, although there are also different types of oil and gas. The fuels sold in conventional stores, however, always meet certain standards, which is why these differences can be better calculated.
Fuel | Net calorific value (MJ/kg) | Gross calorific value (MJ/kg) |
Wood | 14.4 - 15.8 | 15.56 - 17.03 |
Heating oil | 40 | 45.40 |
Natural gas | 32 - 45 | 35 - 46 |
Wood pellets | 17.3 | 38.99 |
Efficiency of condensing boilers
In advertising, an efficiency of over 100% for condensing technology is often stated. However, this does not mean that you get more energy out than you have fed into the heating circuit. In fact, these manufacturer values do not take into account the unavoidable losses in the physical system and are therefore more of a theoretical nature.
However, when it comes to retrofitting or building a new building, it is crucial that old non-condensing heating systems often do not exceed 70 to 80% of the gross calorific value. The efficiency losses of modern condensing technology, on the other hand, are in the single-digit percentage range.
What expenditure in terms of time and materials do you have to expect?
In addition to the heating technology used, the design of the flue stack is decisive because modern systems can preheat the intake air and thus reduce the amount of energy required to warm the air before combustion.
When retrofitting condensing technology, a new flue stack is often unavoidable because acid and moisture-resistant materials are required for the pipes. Common solutions rely on stainless steel or ceramics.
If an existing flue stack cannot be renovated without great effort, a separate, new flue stack can be fitted to the facade. In addition to the costs of approx. € 1,000 to € 3,000 for the flue pipe, the conversion also requires investment of another € 3,000 to € 6,000 for the heat generator. On the other hand, the remaining infrastructure of the system can generally still be used.